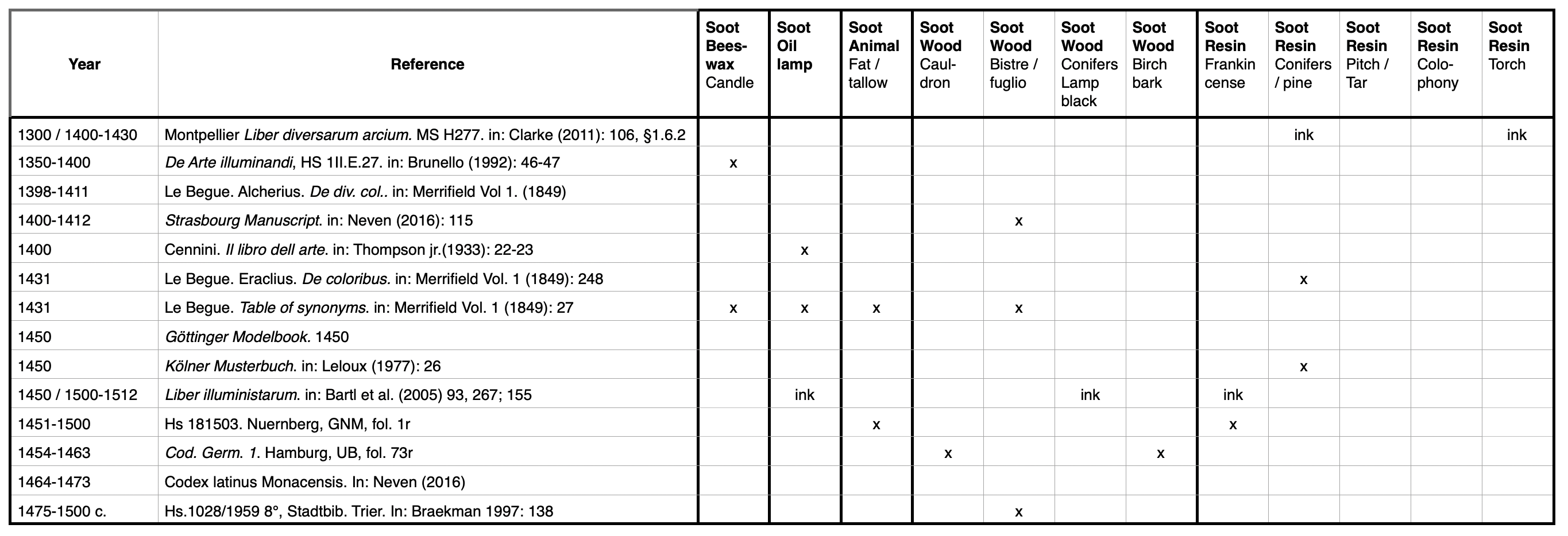
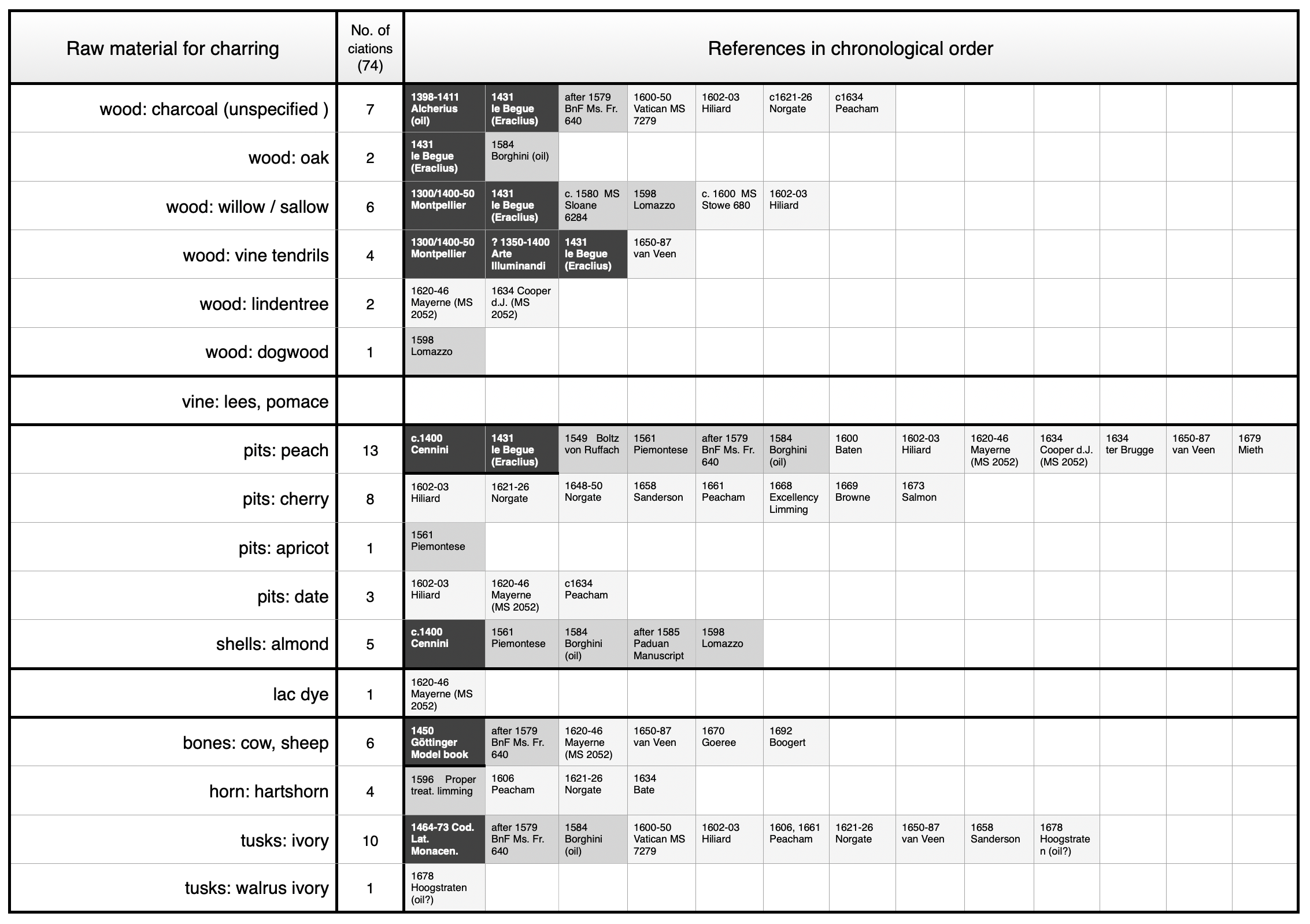
Soot is the reaction product of incomplete combustion (burning) of organic, carbonaceous materials. Many carbohydrates, like for instance wood or fat, burn easily. They act as fuel. The following five groups of raw materials comprise the major sources of soot in pigment production: (1) beeswax, (2) oil, (3) tallow, (4) wood and (5) resins.
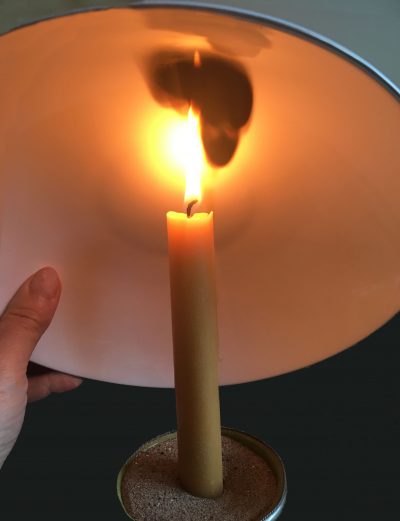
In the presence of oxygen (air) and an external source that provides sufficient energy to start igniting (e.g., tinder, match, lighter), a flame is created. As soon as the process is self-supporting, the fuel is thermally decomposed and forms a variety of gaseous reaction products which further react and finally form the ultimate end products of combustion: water and carbon dioxide. During this process, energy is released as heat and light. The orange-yellow light in the upper part of a flame indicates that the organic material, e.g., candle wax or wood, is in the process of burning. The color is induced by an intermediate product, soot, consisting of pure carbon particles.[1] These particles anneal and therefore remain visible in the flame. If the burning process is interrupted in precisely that state (incomplete combustion), for instance by introducing a metal spoon into the orange-yellow part of a candle flame, or by placing a fire-proof bowl close above the flame, soot deposits on the cold surface (Figure 3). This process is many times described in historic sources to produce black soot pigments. The cold surface should be very smooth, otherwise the fine soot particles are difficult to remove after cooling when the soot is collected by sweeping it off with a feather or by brushing. Large-scale production of so-called lampblack that started with the increasing demand for printing ink from the sixteenth century onwards used a specific technique. To achieve a maximum yield, it combined a low burning fire of resin-rich wood parts with a horizontal chimney to create a fractioned precipitation of soot particles in a special chamber. This allowed for separating soot qualities, ranging from the most expensive pure, deep black soot to cheap and impure products.
Soot has the advantage that the particles are already so extremely fine that they do not require additional grinding, in contrast to most other raw materials. Soot particles are very light and float on the surface of water, where they form clusters. They are static and do not easily disperse in water. Preparation of a good-quality soot-based watercolor or ink requires a binding medium that enables homogeneous dispersion. Thorough dispersing through mixing the binding media with the soot provides the best quality. This is usually done with a muller on a stone.[2]
Depending on several factors, often not only soot particles, but other volatile by-products, especially tar-related products, as well as inorganic ashes precipitate together with the soot. If tar-related impurities are present, the color of the final product tends towards brown shades rather than black. While pure soot consists of pure carbon which is ambiguous for identification of its origin, contaminations might provide evidence to infer the raw material used to produce the soot. The interaction with aqueous media can be negatively influenced due to the hydrophobic nature of many tars. These impurities could be removed by washing in solvents or by applying a subsequent burning step, as elaborately tested by Lewis.[3]
[1] Chylek, P. et al. 2015. ‘Soot’: p. 86–91.
[2] Another technique to achieve proper dispersion is kneading a soot-binder dough, which can take up to one hour. This is the historic production method for middle- and far Eastern soot-based inks. Reissland and Hoesel. 2019. Manuscripts from Yemen 1786-1937: Analysis of glittering particles and ink composition: p. 7.
[3] Lewis. 1763. Commerzium Philosophico-Technicum: p. 341-343.
[1] Chylek, P. et al. 2015. ‘Soot’: p. 86–91.
[2] Another technique to achieve proper dispersion is kneading a soot-binder dough, which can take up to one hour. This is the historic production method for middle- and far Eastern soot-based inks. Reissland and Hoesel. 2019. Manuscripts from Yemen 1786-1937: Analysis of glittering particles and ink composition: p. 7.
[3] Lewis. 1763. Commerzium Philosophico-Technicum: p. 341-343.